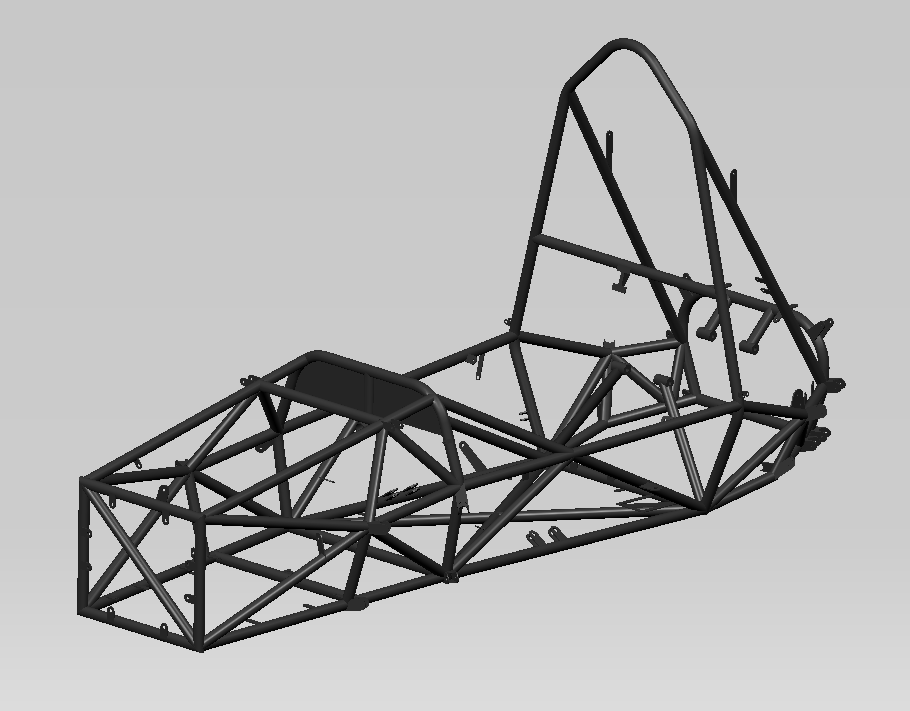
Torsional Stiffness Validation of a FSAE car
Torsional stiffness is a critical factor for racecars, influencing handling, suspension performance, and overall vehicle stability. The objective of this project was to assess the torsional stiffness of the FSAE chassis through FEA simulations and validate the results against physical testing.
In the FEA simulation, a known torque was applied at the front axle while the rear axle remained fixed. We calculated the angular deflection of the chassis model over a range of torque values from 1000 Nm to 10,000 Nm, with the simulated torsional stiffness coming out to be 1129 Nm/degree.
For the physical test, I designed and fabricated a custom Torsion Test Rig to constrain the chassis and apply torque while measuring angular deflection. To eliminate unwanted deflections, the suspension springs were replaced with solid links matching the original suspension geometry.
Torque was applied using weights, and laser pointers mounted on the chassis were used to measure the angular deflection against a screen placed 10 feet away, increasing measurement accuracy by a factor of 9 compared to standard deflection gauges. The measured Torsional Stiffness value was 942 Nm/degree.
In conclusion, we achieved a 19.85% absolute error, which was considered acceptable given material and weld joint variations. This validation test provided confidence in the chassis design, striking a balance between weight reduction and structural integrity, critical for optimizing performance in competition. Click HERE to see the detailed report.
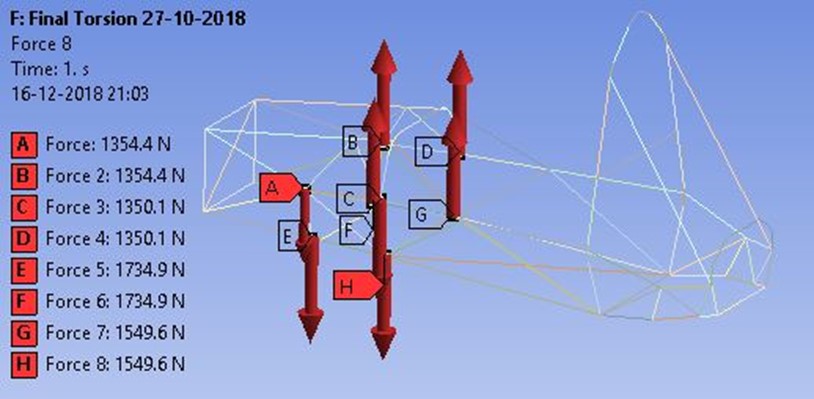
Torque Load at Front Suspension
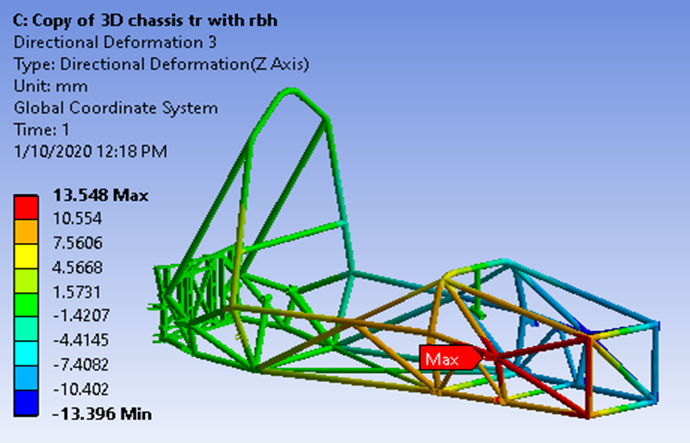
Simulated Deformation
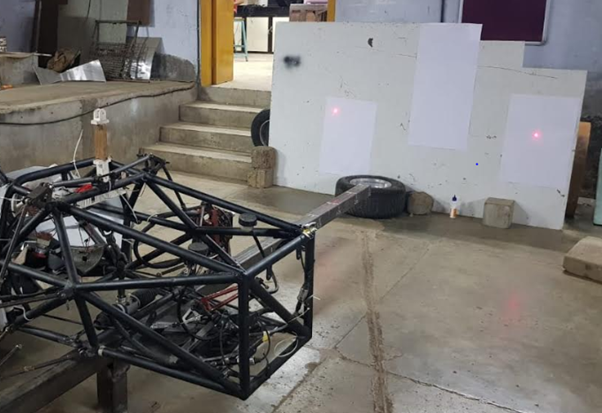
Laser pointers on White Screen
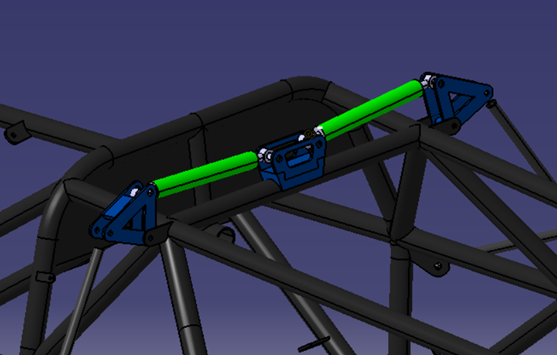
Dummy Dampers to eliminate suspension play

Angular Deflection Measurement Triangle

Torque vs Angular Deflection
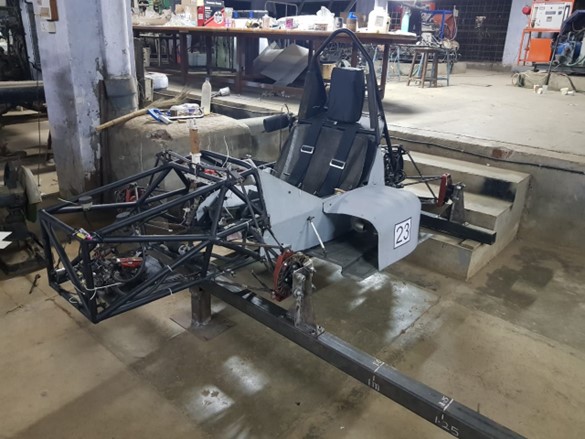
Test Rig setup
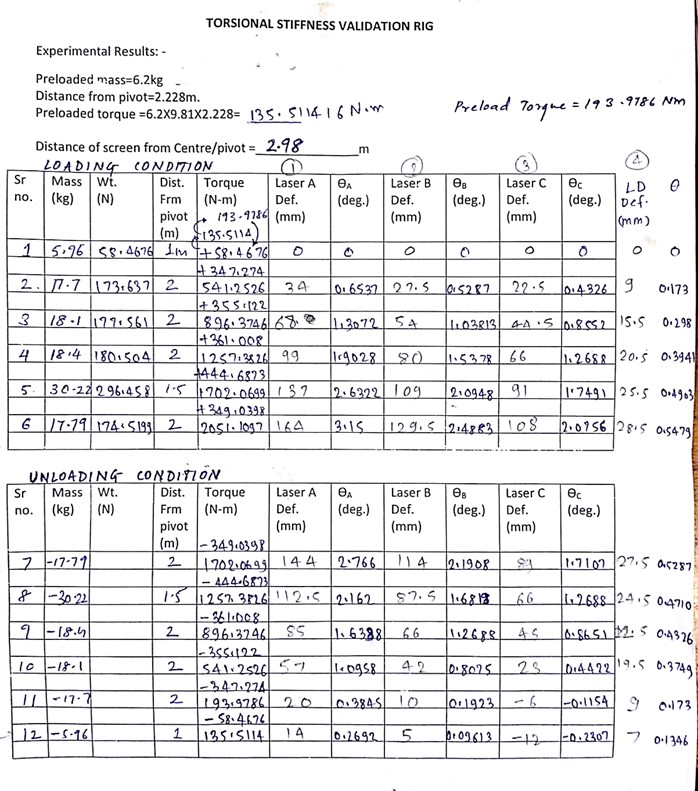
Test Data Collection for Loading and Unloading
Top Skills Applied
My other projects at SPCE Racing
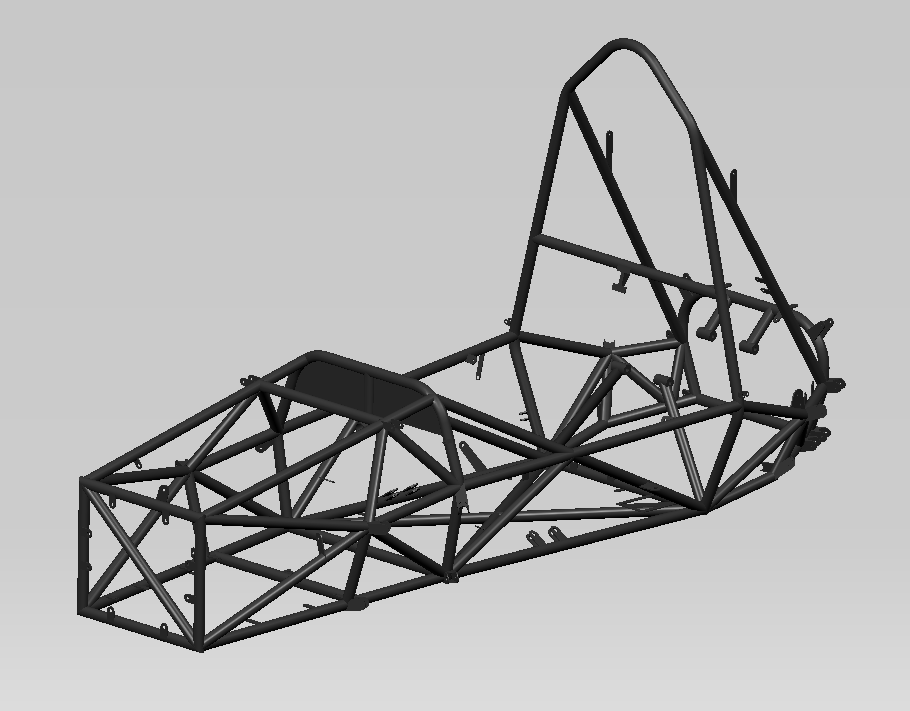
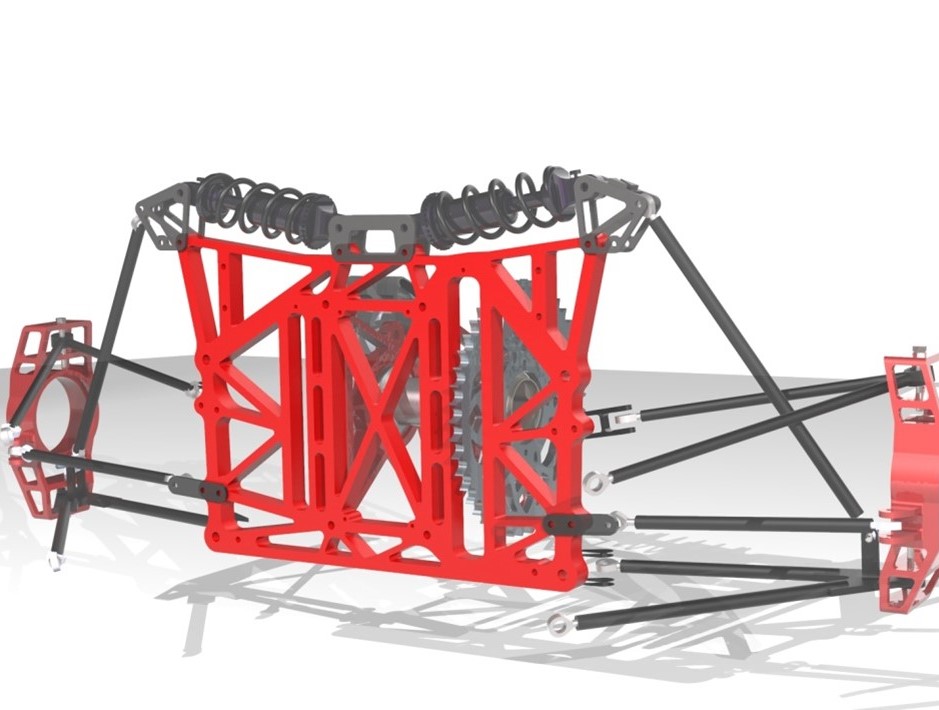
FSAE Aluminium Bulkhead
SPCE Racing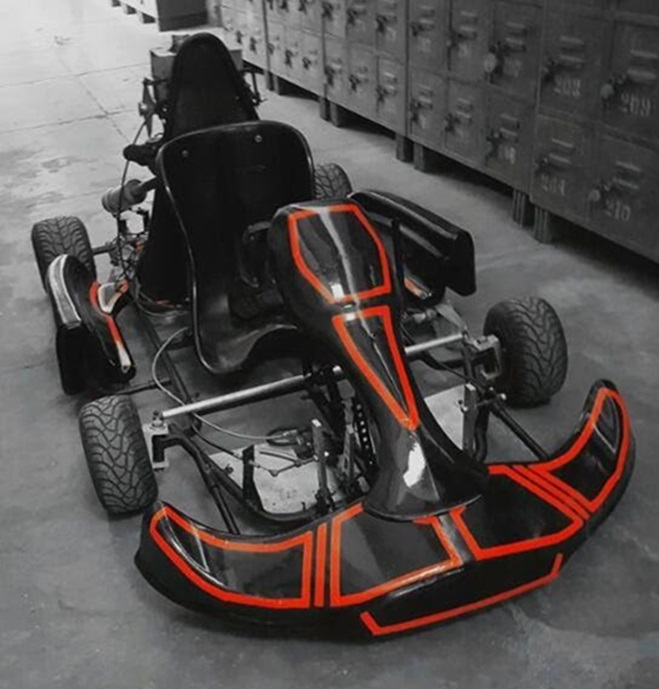